Unplanned downtime is a major productivity killer in manufacturing, but IoT-enabled smart sensors offer a powerful solution—cutting downtime by up to 30% through real-time monitoring, predictive maintenance, and automated alerts. By continuously collecting data from critical equipment, smart sensors enable early detection of issues, reduce response times, and prevent costly breakdowns. This article explores how smart sensors work, common causes of downtime, practical use cases, and key implementation considerations such as system integration, scalability, and workforce adoption. For operations managers and plant leaders, investing in IoT is a strategic move that boosts efficiency, lowers maintenance costs, and drives measurable ROI—paving the way for smarter, more resilient production systems.
Introduction
In manufacturing, unplanned downtime is a costly headache that disrupts production and erodes the bottom line. One study estimated that unplanned downtime costs industrial manufacturers around $50 billion annually. On a plant level, the average facility loses 5–20% of its productive capacity each year due to outages and stoppages. In fact, equipment and process failures account for roughly 80% of all downtime in manufacturing. Beyond lost production, the financial hit is severe – industry analyses peg the average cost of an hour of downtime at about $260,000 (when considering lost output and labor), and in some cases a single downtime incident can cost millions. These numbers highlight why minimizing downtime is such a high priority for operations managers and plant directors.
Looking to cut manufacturing downtime by 30%?
Discover how IoT smart sensors can transform your maintenance strategy. Monitor machines in real time, predict failures before they happen, and keep production running smoothly with data-driven insights.
Let us help you reduce unplanned downtime and boost plant performance.
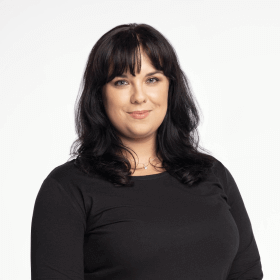
Let us help you reduce unplanned downtime and boost plant performance.
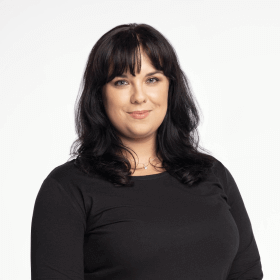
Fortunately, the rise of the Industrial Internet of Things (IIoT) offers a promising antidote to this challenge. By outfitting equipment with smart sensors and connecting them through IoT platforms, manufacturers can continuously monitor machine health, predict failures, and respond faster when issues arise. Early adopters have reported dramatic improvements – for example, advanced IoT analytics can reduce equipment downtime by 30–50% through early warning of breakdowns. Global leaders like Siemens have leveraged AI-driven IoT maintenance to cut downtime by up to 30% in their factories. In this article, we will explore how IoT-enabled smart sensors achieve these gains. We’ll start with a brief overview of what smart sensors are and how they work, then examine common causes of downtime and the specific ways IoT sensors help reduce unplanned stoppages. We’ll also look at a hypothetical use case of a manufacturer implementing sensors to cut downtime, discuss practical considerations for implementation (integration, scalability, security, workforce training), and outline the potential ROI and strategic benefits. The goal is to provide clear, actionable insights into how digital sensor technologies can improve uptime by ~30% or more, in language accessible to industry professionals looking to boost productivity.
What Are Smart Sensors and How Do They Work?
Smart sensors are modern sensor devices that not only measure physical conditions but also have built-in intelligence and connectivity. At a minimum, a smart sensor unit includes the sensing element (to detect parameters like temperature, vibration, pressure, etc.), an onboard microprocessor for processing data, and a communication module (often wireless) to transmit data in real time. In other words, the sensor itself can convert raw readings into useful information and then share it with other systems over networks. Traditional sensors might simply send an analog signal to a controller, but a “smart” sensor can filter noise, run diagnostics, and report data digitally to the cloud or a central platform. This means smarter sensors can calibrate themselves, adjust for environmental factors, and communicate efficiently – all without human intervention at the sensor level.
Example of an IoT smart sensor architecture: Smart sensors on industrial equipment (left) transmit data wirelessly to a local gateway, which relays the information to an IoT cloud platform and user interface (right). This allows real-time monitoring and analysis of machine health from anywhere.
In a manufacturing setting, smart sensors come in many forms and serve diverse purposes. Common examples include temperature and pressure sensors (to ensure machines aren’t running too hot or under dangerous pressure), vibration and acoustic sensors (to detect early signs of mechanical wear or imbalance), proximity and optical sensors (for monitoring positions of parts or detecting defects), and power/current sensors (tracking electrical loads and motor health). These devices might be retrofitted onto legacy equipment or built into new machinery. Once deployed, they continuously capture data about equipment conditions or process parameters and send that data through the IoT network. Some sensors connect via industrial wireless protocols (like Wi-Fi, Bluetooth, or LoRaWAN) or wired interfaces (Ethernet, industrial bus systems) to an IoT gateway on-site; the gateway aggregates data and forwards it to an IoT platform (which could be on the cloud or on-premises servers). Other sensors may integrate directly with existing control systems – for instance, using standards like OPC UA or Modbus to feed data into a SCADA/MES system. The key is that all these sensors collectively provide a live stream of “small data” from the factory floor, which is then aggregated into “big data” for analysis.
What makes these sensors especially powerful is their ability to enable real-time visibility and control. Smart sensors essentially give machines a voice to report on their own status. Factories are using them to get a 360-degree view of operations in real time. For example, smart temperature sensors will automatically alert if a machine is overheating, and can even trigger cooling systems or a safe shutdown. Smart vibration sensors continuously listen for abnormal vibrations in motors or bearings – detecting subtle changes that human operators might miss – and signal when a component is at risk of failure. Sensors can also be tied into process control: if product quality metrics (e.g. fill level, dimension, or color) deviate from the target, the sensor data can feed into automated adjustments on the production line to correct the issue. In the past, an operator might manually gauge these parameters and tweak settings; now the sensors and connected controllers can do it on the fly. In summary, smart sensors are the foundational technology of IoT in manufacturing – they collect data at the source, do some local processing, and then network that data to wherever it’s needed (maintenance teams, cloud analytics, control systems), enabling a proactive and data-driven approach to managing production.
Main Causes of Downtime
Before diving into how IoT sensors reduce downtime, it’s important to understand what typically causes downtime on the factory floor. Manufacturing downtime can be either planned (scheduled maintenance, changeovers, etc.) or unplanned (sudden failures, errors, bottlenecks). Here we focus on the main causes of unplanned downtime, which is what we want to minimize:
- Equipment Failures and Breakdowns: The most common culprit for unplanned downtime is machinery or equipment failure. This could be due to wear and tear, a critical part breaking, lubrication issues, or unforeseen stress on the machine. Studies show that the vast majority of downtime events – around 80% – are triggered by equipment or process failures on the line. For example, a pump motor might overheat and seize up, or a conveyor’s gearbox might fail, causing the whole line to stop. Since modern plants rely on many interdependent machines, a single point of failure can idle an entire production line.
- Poor Maintenance Planning (Reactive Maintenance): Lack of preventive maintenance or inefficient maintenance practices are a major factor behind equipment-related downtime. If machines aren’t serviced at appropriate intervals, minor issues can snowball into major breakdowns. Conversely, performing maintenance too late (or not at all until failure) leads to more frequent outages, while performing it too often can waste downtime unnecessarily. Many unplanned maintenance shutdowns happen because of the absence of a good preventative maintenance program. For instance, failing to replace a worn bearing during scheduled downtime might result in that bearing failing unexpectedly mid-production. Inadequate maintenance planning also includes poor documentation of machine condition, not having the right spare parts on hand, or underestimating the time needed for repairs – all of which can prolong downtime when a failure occurs.
- Human Error and Operational Mistakes: People are integral to production, but mistakes happen – and they can stop production just as effectively as a machine fault. Operator error or human intervention issues are common causes of downtime. This can range from an incorrect machine setup, to pressing the wrong button, to neglecting to notice an alarm. For example, an operator might load a machine improperly causing it to jam, or a maintenance technician might install a part incorrectly, leading to another shutdown. Human errors can also compound other issues (e.g. miscommunication during shift handovers, or slow response to a warning). Training and standard procedures are critical to reduce these, but they remain a factor.
- Quality Control Problems: If production starts drifting out of spec or producing defective products, it often requires halting the line to fix the problem. Quality issues can stem from many sources (defective raw materials, process parameter deviations, equipment calibration issues, or human error in the process). While some quality problems just result in scrap or rework off to the side, others will force a line stoppage until the root cause is addressed. For example, if a filling machine in a beverage factory starts mis-filling bottles, the line might be stopped to prevent thousands of off-spec bottles. Downtime due to quality checks, re-calibration, and rework can be significant if issues aren’t caught early.
- Planning and Scheduling Issues: Inefficient production planning can also cause downtime or idle time. For instance, if there’s a misalignment in production schedules or a poor demand forecast, you might run out of materials or have to wait on upstream processes. Another scenario is unoptimized changeovers – switching a line from one product to another. Changeovers and setups inherently cause some downtime, but if not streamlined, they can take longer than necessary (equipment adjustments, cleaning, etc.). While some of this is planned downtime, poor planning can turn it into excessive downtime. Similarly, not allocating enough staff or resources to a shift can lead to stops when a station can’t operate.
- External Factors (Less Controllable): There are also downtime causes outside the immediate production process, such as supply chain disruptions (if key components or raw materials don’t arrive on time) or external events like power outages, IT system crashes, or environmental disasters. These can halt production even if your equipment and people are perfectly prepared. While smart sensors can’t prevent a citywide power outage, some IoT solutions (like smart energy management or backup power monitoring) might mitigate their impact. However, for the scope of this discussion, we’ll focus on the first four categories above, which are the areas IoT sensors can directly influence.
In summary, unplanned downtime usually boils down to equipment failures, maintenance gaps, operator mistakes, or process issues. Any comprehensive strategy to cut downtime must address these root causes. This is precisely where IoT smart sensors come into play – by tackling equipment and process issues proactively, and even helping operators and maintenance teams avoid mistakes. In the next section, we’ll see how smart sensors target each of these causes to keep production running smoothly.
How Smart Sensors Reduce Downtime
IoT-enabled smart sensors can significantly reduce unplanned downtime by attacking the problem from multiple angles. They monitor equipment in real time, enable predictive maintenance, provide instant alerts and diagnostics, improve quality control, and support process optimization. Below are the key mechanisms through which smart sensors help cut downtime (by as much as 30% or more):
- Real-Time Equipment Monitoring: Smart sensors continuously track the health and performance of machines, giving operators up-to-the-moment visibility. This real-time monitoring means that emerging problems can be caught immediately – long before they cause a failure. For example, vibration sensors on a rotating machine will detect an abnormal spike in vibration (perhaps indicating an imbalance or a worn bearing) and flag it to maintenance staff. Instead of waiting for the machine to break, the team can intervene at the first sign of trouble. Likewise, temperature sensors might alert if a motor is running hotter than normal (a possible precursor to overheating). By aggregating sensor readings on dashboards, engineers have a live view of equipment status across the plant. This helps in two ways: (1) operators can take quick corrective action to prevent a breakdown (for instance, adjusting operating parameters or scheduling a quick fix at the next convenient pause), and (2) even if an issue doesn’t immediately stop the line, they can plan for a fix during planned downtime, thereby avoiding an unplanned stop. Real-time monitoring essentially acts as an automated, tireless set of eyes on every machine, catching anomalies that humans might miss during periodic manual inspections. Studies note that IoT sensors can even detect subtle issues like excess vibrations that would lead to unplanned downtime if unchecked. By reacting to those signals, plants can limit downtime to the absolute minimum needed to address the issue.
- Predictive Maintenance: Perhaps the biggest contribution of IoT to uptime is enabling a shift from reactive maintenance to predictive maintenance. Predictive maintenance uses sensor data and analytics to predict when equipment is likely to fail, so that maintenance can be performed just in time to prevent the failure. Smart sensors feed data (like vibration trends, temperature over time, oil pressure, etc.) into machine learning models or threshold-based algorithms that estimate the remaining useful life of components. This allows maintenance to be scheduled at optimal times – neither too early (which would cause unnecessary downtime and cost) nor too late (which would result in a breakdown). The impact on downtime is huge: instead of the machine failing unexpectedly, you service it during a planned stop. Research by McKinsey & Co. found that IoT-enabled predictive maintenance can reduce unplanned downtime by up to 45%. In practice, this means if a machine historically would break down, say, 10 times a year, sensors and predictive analytics might cut that to only 5 or 6 minor planned interventions. Fewer breakdowns directly equate to less downtime. Additionally, predictive maintenance tends to maximize asset uptime and reliability – machines are more often available and running in good health. Many plants implementing IoT-based predictive maintenance have seen dramatic results; for instance, advanced analytics can predict a machine breakdown well in advance and reduce overall downtime by 30–50% through timely intervention. In short, smart sensors enable a “repair before failure” approach: they warn you that “Pump #3 will likely fail in 10 days”, so you can fix Pump #3 in an orderly way this weekend, instead of it crashing in the middle of a production run next week.
- Automated Alerts and Diagnostics: Smart sensor systems don’t just quietly collect data – they actively alert the team when something’s wrong. IoT platforms can be configured to send real-time notifications (to computers, HMIs, or even technicians’ mobile devices) the moment a sensor reading goes out of acceptable range. These automated alerts ensure that the right people know about an issue instantly, which speeds up response and can prevent a minor issue from escalating. For example, if a pressure sensor on a boiler hits a critical threshold, the system might trigger an alarm and send a text/email to the maintenance supervisor immediately, prompting an investigation or automatic safety shutdown. This level of responsiveness can cut down the reaction time to problems – which is a key part of the downtime equation. The faster you address a problem, the less downtime you accumulate. Moreover, IoT alerts can be tied to automated diagnostics. When a sensor triggers an alert, the system can also log diagnostic data (error codes, the sequence of events, recent sensor readings) to help pinpoint the issue. This guides maintenance crews directly to the root cause. Instead of spending hours troubleshooting, technicians can often identify what’s wrong more quickly, thereby reducing the Mean Time to Repair (MTTR). For instance, an IoT monitoring platform might not only alert that “Machine X’s spindle vibration is high” but also indicate “vibration in frequency range suggesting bearing wear.” Armed with this info, the team brings the right replacement bearing and fixes the issue in a short maintenance window. Automated alerts and notifications have been shown to reduce downtime by facilitating off-hours maintenance and quicker interventions, so that fixes can be made without interrupting peak production. In summary, smart sensors serve as an early warning system and guide, ensuring that no critical condition goes unnoticed and that repairs are efficient.
- Quality Assurance Insights: IoT sensors can also reduce downtime by improving quality control and reducing the chance that quality problems will require line stoppages. As mentioned, sensors monitor process variables (like temperature, humidity, alignment, speed, fill levels, etc.) that affect product quality. By analyzing this data in real time, manufacturers can catch deviations before they result in large batches of defective product. This has two benefits: (1) You avoid the scenario of producing a lot of defects and then having to halt production to troubleshoot and recalibrate. And (2) by maintaining consistent quality, you avoid unplanned downtime for investigations or rework. For example, consider a painting booth in an auto parts plant – if a humidity sensor detects that air moisture is out of the acceptable range for paint adhesion, it can alert operators or automatically adjust the climate control, preventing a bad batch that would force a line clean-up later. Similarly, vision sensors with AI might detect a minor trend of dimensional drift in machined parts and prompt a tool adjustment before the parts go out of spec. Essentially, smart sensors ensure process parameters stay within optimal ranges, which means the process doesn’t need to be stopped as often for quality checks or fixes. Over time, the data from these sensors also provides insights for quality improvement: engineers can analyze patterns to find root causes of recurring quality issues and address them proactively. This continuous improvement loop reduces both scrap and downtime. In industry practice, smart sensor deployments often yield multi-faceted benefits – they reduce downtime, improve machine performance, enable predictive maintenance, and also improve product quality and throughput. All of these outcomes are interconnected: a smoother-running process produces better quality, and good quality in turn means fewer stoppages. Thus, IoT sensors contribute to uptime by keeping quality-related interruptions at bay, while simultaneously boosting yield.
- Process Optimization and Bottleneck Reduction: Beyond direct maintenance and quality, the big data collected from IoT sensors can be analyzed to optimize the overall production process, which in turn reduces downtime or idle time. By aggregating data from many sensors (across multiple machines and lines), manufacturers can identify patterns and inefficiencies that weren’t visible before. For instance, analysis might reveal that a particular machine experiences small 2-minute micro-stops 10 times a day due to minor jams – something that wasn’t always reported. With that insight, engineers can investigate and fix the underlying cause (maybe a sensor that triggers a false positive jam signal, or a part that needs lubrication), thereby eliminating those micro-stops and reclaiming that lost production time. IoT platforms often include advanced analytics and dashboards that help managers pinpoint bottlenecks or underperforming assets. According to research, using advanced data analytics on IoT sensor data can predict issues before they occur and suggest optimizations, potentially reducing overall downtime by up to 50% while also extending equipment life. An example of process optimization could be using sensor data to better synchronize production line speeds: if one station is slower and causing downstream stations to wait (idle time is also a form of downtime), data might highlight this imbalance so you can adjust cycle times or add buffer capacity. Another example is optimizing maintenance schedules across multiple machines – by using IoT data on all equipment, you might consolidate maintenance activities into a single planned downtime event (servicing several machines at once) rather than separate stops, thus reducing the total downtime. In short, IoT-driven analytics helps plants run leaner and with higher Overall Equipment Effectiveness (OEE). Process improvements might not always be as headline-grabbing as a major breakdown prevented, but cumulatively they can add up to a significant reduction in lost time. And importantly, these optimizations often come from insights that only emerge when you have a wealth of sensor data to analyze.
Looking to cut manufacturing downtime by 30%?
Discover how IoT smart sensors can transform your maintenance strategy. Monitor machines in real time, predict failures before they happen, and keep production running smoothly with data-driven insights.
Let us help you reduce unplanned downtime and boost plant performance.
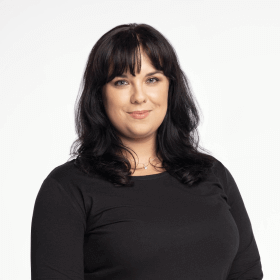
Let us help you reduce unplanned downtime and boost plant performance.
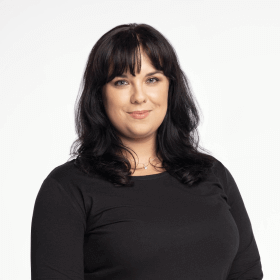
In combination, these five capabilities of smart sensors – real-time monitoring, predictive maintenance, instant alerts, quality control, and process analytics – create a powerful feedback loop that keeps manufacturing operations on track. Instead of operating blindly and reacting to failures, factories become proactive and data-driven, addressing issues on their own terms. The end result is that unplanned downtime becomes far less frequent and less severe. In the next section, we’ll illustrate how these concepts come together in a realistic use case of a manufacturer deploying IoT sensors to cut downtime by ~30%.
Hypothetical Use Case Examples
To make this more concrete, let’s consider a hypothetical scenario of a manufacturing company implementing IoT smart sensors to reduce downtime. Axis Components Ltd. is a fictional mid-sized manufacturer of industrial components (let’s say they produce metal and plastic parts for automotive and aerospace clients). Axis operates a plant with several production lines containing equipment like injection molding machines, CNC machining centers, and assembly stations. They have been facing challenges with unplanned downtime – machines would break down unexpectedly or processes would be halted to address quality issues, leading to missed production targets. Their average unplanned downtime was around 50 hours per month, spread across various machines, which was roughly 10% of available production time. Axis’s operations manager and plant director decide to pilot an IIoT smart sensor program to tackle this issue.
Initial Challenges: Axis Components identified two chronic problem areas contributing to downtime. First, their injection molding machines often suffered breakdowns due to wear in the hydraulic system – sometimes a pump would fail with little warning, taking a machine out for a full day. Maintenance was mostly reactive; the team fixed things after they broke. Second, on their assembly line, they experienced periodic stops because of quality defects – for example, an automated screwdriver station would occasionally apply the wrong torque, leading to loose screws that triggered a quality check downstream and a line stoppage to fix the tool calibration. These issues were costing Axis orders (delays in delivering parts) and significant overtime expenses.
IoT Implementation: Axis launched a pilot by equipping three critical injection molding machines with smart sensor kits. Each machine got vibration sensors on the pump motors, temperature sensors on the hydraulic oil and motor bearings, and power sensors monitoring motor current draw. These sensors were connected to a local IoT gateway, which streamed the data to Axis’s new cloud-based IoT analytics platform. At the same time, on the assembly line, they installed a couple of smart torque sensors and position sensors on the screwdriver station and integrated those with the line’s PLC and IoT system to monitor each fastening operation’s torque in real time. The IoT platform was configured with predictive analytics: it learned the normal vibration signature of the molding machine pumps and set up thresholds/trends for early warning (for instance, a slow rise in vibration at a certain frequency band indicating bearing degradation). They also set up automated alert rules – if any sensor readouts went beyond normal limits (say, oil temperature too high, or an assembly screw torque deviating from spec), the system would send an instant alert to maintenance technicians via a mobile app and also flag it on a big screen dashboard in the control room. Importantly, Axis made sure to integrate this IoT platform with their existing systems: maintenance personnel got alerts through their existing work order system (so an IoT alert could automatically generate a maintenance ticket), and production supervisors could see IoT data alongside their MES (Manufacturing Execution System) displays for a unified view.
Results after Implementation: In the months following these upgrades, Axis Components saw noticeable improvements. The vibration sensors on the injection molders started paying off within weeks – on one machine, the sensor data showed an unusual spike in vibration and heat in the hydraulic pump motor. The predictive analytics indicated a high likelihood of pump failure within the next couple of weeks. The maintenance team received an alert and decided to proactively replace the pump over a scheduled downtime weekend. When they inspected the old pump, they found it was indeed on the verge of failing. By catching it early, they avoided at least 16 hours of unplanned downtime that a mid-week breakdown would have caused. Over a year, such predictive maintenance interventions on multiple machines reduced unexpected outages significantly. Axis logged 7 fewer major breakdowns that year compared to the previous year. In terms of numbers, their unplanned downtime on those pilot machines dropped by roughly 30%, contributing to an overall plant downtime reduction of about 20% (noting they hadn’t yet instrumented every single machine).
On the assembly line side, the smart torque sensors eliminated the mystery around the screwdriver issue. The IoT system revealed that on certain product models, the screwdriver was occasionally not achieving the programmed torque (perhaps due to a software glitch or variance in screw material). Each time that happened, an alert would fire, and the operator could immediately stop that unit from moving forward and re-torque it, preventing a downstream quality failure. They also identified the root cause and fixed the programming after seeing the pattern in the data. The result was the assembly line experienced far fewer full stoppages – what used to be a weekly downtime event to fix a batch of mis-torqued screws became a rare occurrence. This improved their throughput and on-time delivery.
Broad Benefits: By the end of the pilot year, Axis Components Ltd. had cut total unplanned downtime by about 30% in the areas where sensors were implemented, and they estimated an overall 15% increase in OEE (Overall Equipment Effectiveness) for those lines. In practical terms, this translated to hundreds of extra production hours gained over the year. Because machines were failing less, maintenance costs went down as well – emergency repair overtime was reduced and parts were replaced in a controlled manner (often before catastrophic damage). Quality metrics improved (scrap rate dropped by 10% in the assembly area due to catching issues early). Axis also noted a cultural change: operators and technicians started to trust the sensor system and used it as a tool – they would check the live dashboards at the start of each shift and felt more in control, rather than always being in firefighting mode. Encouraged by the pilot’s success, the plant director planned to scale the IoT sensor program to more equipment and additional lines, aiming for even higher uptime and efficiency gains across the facility.
While this Axis Components example is fictional, it reflects realistic outcomes reported by manufacturers adopting IoT solutions. The key takeaways are that smart sensors enabled Axis to detect issues early, fix problems on a scheduled basis, and learn from the data to optimize their processes. The end result was a significant reduction in downtime and a clear positive ROI (in this scenario, the savings from avoided downtime and improved output far outweighed the cost of sensors and the IoT system within the first year). Next, we will discuss some important considerations Axis (and any company) would need to keep in mind when implementing such IoT solutions in a real-world manufacturing environment.
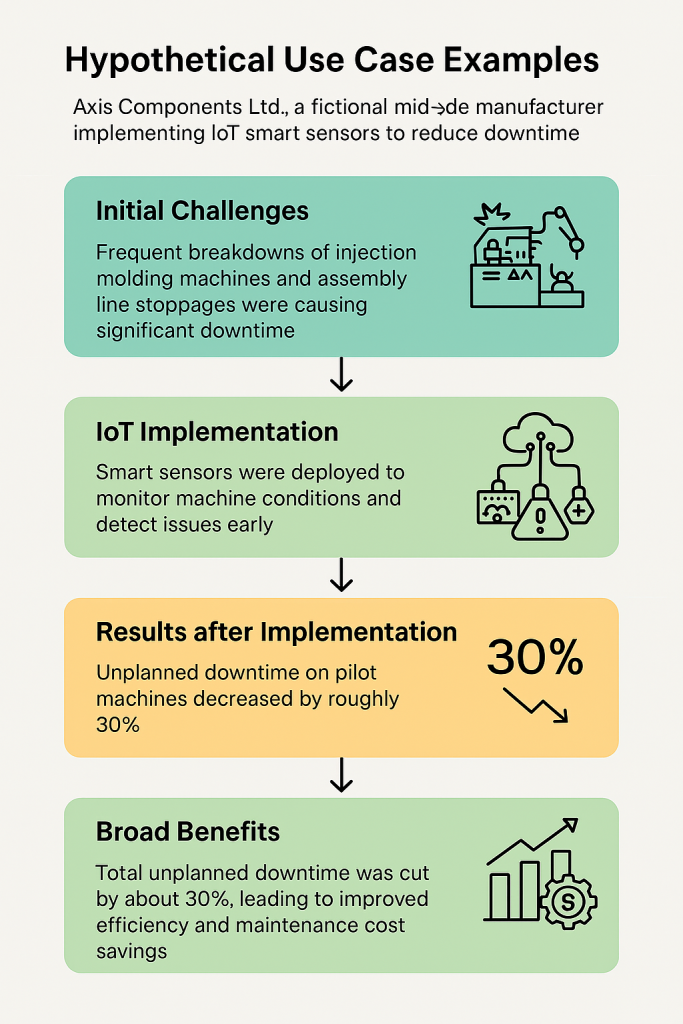
Implementation Considerations
Implementing IoT smart sensors in a manufacturing setting is not as simple as sticking sensors on machines and walking away – it requires careful planning to integrate with existing operations and to ensure the solution is scalable, secure, and embraced by the workforce. Here are some key considerations for a successful rollout:
- Integration with Existing Systems (SCADA/MES/ERP): Most factories already have automation and monitoring systems such as SCADA (Supervisory Control and Data Acquisition), MES (Manufacturing Execution Systems), and various ERP or maintenance management systems. A new IoT sensor platform should be integrated so that it complements these, rather than operates in a silo. This often means using standard protocols and APIs to feed IoT data into the existing dashboards or databases. For example, if a plant’s SCADA system is already displaying machine statuses, you’d want the new sensor alerts to appear there too, or in the MES that production managers use for scheduling. Integration may involve IoT gateways that translate sensor data to formats that SCADA/MES can ingest (e.g. using OPC UA servers for sensor data). It’s also important to consider legacy equipment: older machines might not have digital interfaces, so IoT retrofit kits (sensors + edge devices) need to be installed and then bridged to the legacy control system. Many companies start with a pilot project on one line or a few machines and integrate that with their systems to iron out any dataflow issues, before scaling up. The goal is a seamless flow of information – IoT data should enhance the single source of truth for operations. When done right, operators might not even distinguish between “SCADA data” and “IoT data” – it all becomes part of a unified monitoring interface.
- Scalability and Network Infrastructure: An IoT deployment might begin with 10 sensors, but if it proves valuable, you could soon be dealing with hundreds or thousands of sensors across a plant. It’s crucial to design the system with scalability in mind. This includes having a robust network (Wi-Fi, Ethernet, or LPWAN coverage) that can handle the data traffic reliably in an industrial environment (which may have interference, long distances, etc.). You may need to invest in industrial-grade access points or mesh network setups so that even sensors on remote or moving equipment (e.g., an overhead crane) stay connected. The IoT platform chosen (whether cloud-based or on-premises) should be capable of handling big data – not just storing it but quickly processing and analyzing it in real time. Cloud IoT services from major providers can typically scale well, but you must ensure latency is low if real-time control decisions are needed locally (sometimes a hybrid edge computing approach is used: do quick processing near the sensor for immediate control, and send aggregated data to cloud for analytics). Additionally, consider how you’ll manage the devices at scale – provisioning new sensors, calibrating them, and maintaining them (smart sensors themselves might need firmware updates or battery replacements for wireless types). Planning for scalability means thinking a few steps ahead: If this pilot works and we deploy 10× more sensors, can our network, software, and team handle it? It’s wise to choose IoT solutions that are modular and can expand without a complete redesign.
- Data Security and Privacy: Introducing IoT devices and connectivity in a plant raises cybersecurity considerations. Each new sensor or gateway is another node that could be vulnerable if not properly secured. It’s essential to ensure end-to-end security: sensors and gateways should use encryption when transmitting data (to prevent eavesdropping or tampering), and access to the IoT platform must be controlled with authentication and proper user permissions. If the IoT system connects to the internet or cloud, strong firewall rules and possibly VPN tunneling should be in place to protect the plant’s network. Many manufacturers create a segmented network for IoT devices separate from the core operations network, with only carefully managed bridges between them, to contain any security issues. Device management is also key – you need to be able to update passwords, firmware, and revoke access for devices if needed. Additionally, the data being collected (equipment performance data) might be sensitive in some contexts (e.g., data that reveals production rates or proprietary process parameters). Companies should have policies on who can access IoT data and how it’s used. It’s worth noting that a survey of manufacturers found a majority are concerned that IoT technologies introduce higher cybersecurity risks. Therefore, building a secure-by-design IoT architecture and possibly working with IT/OT security experts is a must. The last thing you want is a cyber incident causing downtime, the very outcome you were trying to prevent. Fortunately, most reputable industrial IoT vendors provide robust security features (device authentication, encrypted protocols like MQTT over TLS, etc.), but it’s up to the implementers to configure and maintain them properly.
- Workforce Training and Adoption: Introducing smart sensors and IoT analytics will change the workflows for operators, maintenance technicians, and engineers – and managing this human factor is critical. The best technology will have limited impact if the staff doesn’t trust it or know how to use it. Thus, change management and training are key parts of implementation. Operations and maintenance teams should be involved early, perhaps even in selecting which sensor solutions to use, so they feel ownership. Training sessions should demonstrate how the IoT system works, how to interpret sensor dashboards, and how alerts will be received and acted upon. It’s important to clarify that these tools are there to help the workforce, not to replace them. For example, maintenance crews may initially be skeptical of predictive analytics – “Will the sensor really know when the machine needs service better than my 30 years of experience?” Winning them over might involve showing early wins (e.g., instances where the sensor caught something invisible to the naked eye) and integrating their feedback (maybe they want alerts delivered in a certain way, or they have insights on setting threshold levels). There may also be a need to develop new skills: data analysis and IoT system management could become part of someone’s role (perhaps a reliability engineer or a dedicated “digital transformation champion” in the plant). Providing ongoing support, and perhaps having a few tech-savvy team members specialized in IoT who can assist others, will smooth adoption. Culturally, it helps to celebrate successes – if the IoT system prevented a big downtime incident, communicate that across the plant so everyone sees the value. Over time, as people get comfortable, the workforce tends to become more engaged – operators start suggesting “Hey, can we also put a sensor on Machine B? I think it would help with that other issue,” which is a sign of successful adoption. In summary, people and process adaptation should go hand-in-hand with the technical deployment. Starting with a pilot can also help in this regard: it gives the workforce time to adjust on a small scale before scaling up broadly.
In addition to the above, companies should also consider the cost and ROI analysis during implementation (which we discuss in the next section), data governance (how long to store data, how to ensure data quality), and perhaps compatibility or interoperability if using multiple vendors’ equipment (adhering to IoT standards can help avoid vendor lock-in). By addressing integration, scalability, security, and team readiness, a manufacturing firm can set itself up for a smooth and successful IoT deployment that delivers sustained reductions in downtime.
Potential ROI and Strategic Benefits
Investing in IoT smart sensors and predictive analytics is not just a technical project – it’s a business decision that should yield a strong return on investment (ROI). Fortunately, the case for IoT in reducing downtime tends to be compelling when the numbers are crunched. Here we’ll outline the potential ROI in terms of hard benefits (like production gains and cost savings) as well as broader strategic advantages that digitalization brings.
Direct Downtime Reduction = Production Gains: The most immediate ROI driver is the increase in uptime. Simply put, more uptime means more output. For example, if a factory was averaging 100 hours of unplanned downtime per year and IoT solutions manage to cut that by 30%, that’s 30 hours of extra production time regained. In a high-volume manufacturing environment, 30 hours could mean tens of thousands of additional units produced. In capital-intensive industries, it could mean avoiding lost opportunity to serve customer orders. One way to estimate the value: multiply hours of downtime saved by the value of production per hour. If a plant’s output is worth $10,000 per hour (just as an illustration), saving 30 hours yields $300,000 in additional product output. In many heavy industries, the value per hour is even higher – recall that the average across industries is estimated around $260k per hour of downtime. Even if your facility is below that average, the gains add up quickly. Avoiding a single major breakdown can be like preventing a $1–2 million loss when you account for lost production, rush shipment costs to make up delays, etc. Thus, from a pure throughput perspective, IoT-driven downtime reduction directly boosts revenue potential.
Lower Maintenance and Repair Costs: Another financial benefit is the reduced maintenance expenses that come with smarter maintenance strategies. In reactive mode, a machine failure might cause secondary damage (a broken part damages other components, increasing repair costs) and often involves expedited shipping of spares or calling in outside experts last-minute – all of which are costly. With predictive maintenance via IoT, companies can avoid those scenarios. Parts can be replaced right before failure (preventing collateral damage), and inventory can be managed such that spares are on hand without emergency fees. According to industry research, predictive maintenance can cut overall maintenance costs by around 20–30%. For instance, if a factory spends $1 million a year on maintenance, it might save $200k-$300k by optimizing schedules and preventing big breakdowns. Additionally, equipment that is well-maintained tends to last longer. The same McKinsey study noted that IoT-based maintenance can extend machinery life by up to 20%. This means deferred capital expenditures on new equipment – a strategic financial benefit. Instead of replacing a machine after 10 years, you might get 12 years out of it because it didn’t suffer as much wear-and-tear from catastrophic failures. Extended asset life and fewer emergency repairs both contribute to ROI.
Improved Quality and Reduced Scrap/Waste: While our focus is downtime, it’s worth mentioning that the quality improvements from IoT (fewer defects, more consistent process) have a financial upside too. Less scrap and rework means less wasted material and labor. It also means better customer satisfaction (fewer rejects or recalls), which can translate into repeat business and a stronger reputation. These are somewhat softer benefits but do impact the bottom line over time – and they come as a bonus alongside uptime improvement because the same sensors that help with downtime also often improve quality.
Labor Efficiency and Workforce Empowerment: Another angle is the effect on labor productivity. When machines break down less, workers spend more time producing and less time waiting idle or firefighting issues. The maintenance team can shift from crisis-mode (which often incurs overtime and stress) to a more planned approach, which is generally more efficient and cost-effective. There can be labor cost savings by reducing overtime or even reallocating workforce to more value-added tasks (since the IoT system handles a lot of monitoring, technicians can focus on performing fixes and improvements rather than constantly inspecting equipment). Moreover, the workforce becomes more effective – a maintenance technician armed with diagnostic data can fix a problem in 1 hour that might have taken 4 hours to troubleshoot without data. That productivity gain is a kind of ROI in itself (doing more with the same staff).
Quantifying ROI: Many companies do a business case where they sum up these savings: additional output revenue, maintenance cost reduction, quality improvement savings, etc., and compare against the cost of the IoT implementation (which includes sensor hardware, IoT platform software or subscription, network infrastructure, training, and ongoing support). Often, the payback period for IoT initiatives focused on downtime is quite attractive. It’s not uncommon to see ROI within 1-2 years for well-targeted IoT projects. In fact, IoT project success has improved to the point that over 90% of enterprises report a positive ROI from IoT deployments – and many report seeing returns in under two years. This aligns with anecdotal reports that a small pilot can pay for itself with just one or two prevented downtime incidents. For example, consider a sensor system that costs $100k to deploy on a critical production line. If it prevents a single major breakdown that would have caused a 2-day outage, it might have saved the company $500k in one go (assuming ~$250k per day downtime cost), thereby justifying its cost five times over. And that’s just one incident; over multiple years the cumulative benefits can dwarf the initial investment. Of course, actual numbers will vary by industry and scale, but the point is that the economics tend to be favorable given how expensive downtime is.
Strategic Benefits: Beyond the immediate dollars, implementing IoT and smart sensors brings strategic advantages that position a manufacturer for the future. One major benefit is the creation of a data-driven culture and decision-making. With IoT data, managers can base decisions on real evidence from the factory floor rather than gut feel. This can lead to better strategies in production planning, equipment procurement (knowing which machine models perform best), and continuous improvement efforts. It also fosters a culture of proactive problem-solving – teams start to look at trends and address things before they become problems, which can spill over into other areas of operation (safety, inventory management, etc.).
Another strategic aspect is improved customer reliability and trust. If you dramatically reduce unplanned downtime, you are much less likely to have production delays that could impact customer deliveries. You can confidently commit to tighter delivery schedules or accept more orders, knowing your operations are more reliable. This reliability can be a competitive differentiator – it improves your reputation for on-time delivery and quality. In industries like automotive or electronics, being the supplier who always delivers as promised can win more business. Some manufacturers even turn their operational excellence into marketing points when bidding for contracts.
Adopting IoT in manufacturing is also a step toward full smart factory / Industry 4.0 capabilities. Once the sensor infrastructure and data platform are in place for downtime reduction, the same setup can be extended to other use cases: energy optimization, inventory tracking (with RFID and sensors), predictive quality analytics, or even integration with supply chain systems for end-to-end visibility. In essence, investing in IoT sensors is building a foundation for broader digital transformation. It could enable things like digital twins (virtual models of machines fed by sensor data), more automation (since reliable data can allow certain decisions to be automated), and even new service models (some manufacturers use IoT data to offer condition-based maintenance services or warranties to their customers – although that’s more common for OEMs of equipment). For the plant itself, one side benefit of well-monitored equipment is improved safety: sensors might detect a hazardous condition (like a gas leak, or an overheating part that could cause a fire) and thus prevent accidents, keeping workers safe and avoiding incident-related downtime.
Finally, there is a sustainability angle: a more efficiently run operation with less downtime often uses energy more efficiently and generates less waste. Machines running optimally consume less power and produce fewer off-spec products that go to scrap. Studies have found proactive maintenance can yield energy savings of 5-20% by keeping equipment at peak efficiency. While the question at hand is productivity, it’s worth noting that these improvements align with corporate sustainability goals, which is an increasingly important strategic objective in manufacturing. In a sense, what’s good for uptime is good for the environment too – a win-win that can be highlighted to stakeholders.
When pitching the ROI and benefits to executives, it helps to present both the quantitative gains (e.g. “we expect $X in savings or extra earnings per year, for an investment of $Y”) and the qualitative strategic gains (e.g. “this will position us as a technology leader, improve customer trust, and pave the way for AI-driven production optimization”). As noted earlier, the vast majority of companies now find IoT projects worthwhile, so the question is less “if” it will pay off and more about ensuring you execute the project correctly to capture those benefits.
Conclusion
Unplanned downtime has long been the bane of manufacturing, but with IoT-powered smart sensors, the industry now has a powerful toolkit to combat it. In summary, smart sensors and connected monitoring systems enable manufacturers to predict and prevent many equipment failures, respond faster to issues, maintain consistent quality, and optimize processes – leading to significantly higher uptime. A reduction in downtime on the order of 30% (or even more) is not unrealistic, as demonstrated by both real-world cases and research data. This improvement translates directly into higher productivity, lower costs, and a stronger ability to meet customer commitments.
For operations managers and plant directors, the message is clear: investing in IoT sensor technology and the associated analytics is a smart business move to drive efficiency. However, it’s also important to approach it methodically. Start with well-defined goals (e.g. “reduce downtime on critical line A by 25%” or “implement predictive maintenance for the top 5 failure-prone machines”). Consider starting small with an IoT pilot project on a single line or a single type of equipment. This allows your team to learn and demonstrate quick wins without a huge upfront investment. Many companies find that a focused pilot not only proves the ROI in a microcosm but also helps work out technical kinks and build employee buy-in. Once the pilot shows success, you can scale up step by step – roll out sensors to more machines, integrate more data sources, and expand the predictive models.
Remember to involve your people in the journey – combine the new digital tools with the invaluable practical knowledge of your machine operators and maintenance veterans. IoT data plus human expertise is a powerful combination. Also, collaborate with IT and OT (operational technology) teams to ensure the solution fits your infrastructure securely and seamlessly. Keep an eye on cybersecurity and choose reputable platforms that offer robust security and reliability (downtime monitoring that itself goes down is not helpful!).
As you implement these technologies, you’ll likely uncover additional opportunities for improvement. IoT in manufacturing often starts with maintenance and downtime reduction, but it can evolve into a broader digital transformation of your operations. That can include areas like real-time production optimization, energy management, inventory automation, and more, all feeding into the ultimate goal: a more efficient, flexible, and competitive manufacturing operation.
In closing, IoT smart sensors represent a practical, proven way to attack downtime – one of manufacturing’s most stubborn challenges. With careful implementation, a clear strategy, and openness to innovation, even a traditional plant can turn into a smart factory where machines tell you what they need and downtime is no longer a constant worry. The technology is ready and mature; many peers in the industry are already reaping the benefits. The time is ripe to take a small pilot step toward IoT-enabled maintenance and see the results for yourself. Reducing downtime by 30% or more is a game-changer for productivity, and it’s within reach. By harnessing the insights from smart sensors, operations leaders can keep their production lines humming and drive significant value for their business. The journey to higher uptime starts now – one sensor at a time, one machine at a time, and soon, you’ll wonder how you ever ran the plant without this level of visibility and control.
Let's talk about your IT needs

Let me be your single point of contact and lead you through the cooperation process.
Choose your conversation starter
Signed, sealed, delivered!
Await our messenger pigeon with possible dates for the meet-up.