Business Intelligence (BI) is revolutionizing the manufacturing industry by enabling real-time data analysis, predictive maintenance, supply chain optimization, and quality control. By leveraging BI tools such as Power BI, Tableau, and SAP BI, manufacturers can reduce downtime, enhance efficiency, and make data-driven decisions that lower costs and improve productivity. Case studies show that companies implementing BI achieve significant gains, including a 40% reduction in unplanned downtime and improved inventory management. As AI, IoT, and cloud-based BI solutions continue to evolve, manufacturers that invest in these technologies will gain a competitive edge, ensuring agile, optimized, and future-ready production processes.
Business Intelligence (BI) refers to the technologies and strategies used by organizations to analyze data and deliver actionable information. In manufacturing, BI plays a pivotal role in making sense of vast amounts of production data – from machine performance to supply chain metrics – to drive smarter decisions and efficiency improvements. BI is highly relevant in today’s manufacturing environment, where Industry 4.0 initiatives emphasize data-driven operations and real-time insights. In fact, BI is revolutionizing the manufacturing industry by providing insights that help companies optimize processes and maximize efficiency. According to a Gartner study, organizations that deploy BI solutions increase their profitability by an average of 8–10%, underscoring the tangible impact of BI on the bottom line for manufacturers.
Manufacturing operations are inherently complex, involving numerous variables such as equipment performance, workforce productivity, material supply, and quality control. BI systems gather and consolidate data from across production lines, equipment sensors, and enterprise systems to provide a unified view of these operations. By analyzing this data, manufacturers can spot inefficiencies, predict issues before they escalate, and respond quickly to changing conditions. In short, BI turns raw manufacturing data into actionable intelligence – enabling factories to become more agile, productive, and competitive in a data-driven marketplace.
Ready to optimize your manufacturing processes with Business Intelligence?
Leverage BI solutions to enhance production efficiency, reduce downtime, and gain real-time insights into your manufacturing operations. Let data drive your decision-making and unlock new levels of performance.
Our experts are here to guide you through the implementation of BI in manufacturing.
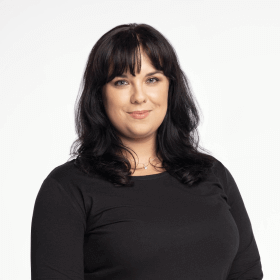
Our experts are ready to help you integrate BI into your manufacturing strategy.
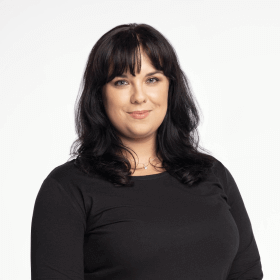
Why Optimize Production Processes?
Optimizing production processes is essential for manufacturers aiming to thrive in a highly competitive and cost-sensitive market. The benefits of streamlining and improving operations go far beyond just making more products – they directly influence a company’s financial performance and market position. Key reasons to focus on production process optimization include:
- Efficiency Gains: Smoother workflows and well-tuned processes mean higher throughput with less waste. This improved operational efficiency leads to increased productivity and shorter production cycles, allowing manufacturers to meet demand faster. By eliminating bottlenecks and reducing idle time, companies can do more with the same resources.
- Cost Reduction: Every inefficiency in production – whether it’s machine downtime, scrap and rework, or excess inventory – carries a cost. Optimizing processes helps identify and cut out these wasteful activities. Manufacturers can reduce material waste, minimize downtime, and lower energy consumption, directly improving their bottom line. Leaner operations also free up capital that can be reinvested elsewhere in the business.
- Competitive Advantage: In today’s market, manufacturers must be agile and responsive. Companies that run highly efficient and data-driven production lines can deliver products faster and at lower cost, which is a significant competitive edge. Optimization enables better quality and consistency as well, leading to greater customer satisfaction. In contrast, firms that neglect process improvement risk falling behind more proactive competitors.
Ultimately, optimizing production processes is about doing things better, faster, and cheaper. It improves profitability (through cost savings and higher output) and helps a manufacturer adapt to changes in demand or market conditions with confidence. When paired with BI tools that provide visibility into all aspects of operations, optimization efforts become far more effective, ensuring that efficiency gains and cost reductions are continually identified and acted upon.
How BI Helps Optimize Production
Business Intelligence provides the data backbone for optimization initiatives in manufacturing. Modern BI tools allow companies to monitor operations in real time, predict and prevent problems, and continuously improve every facet of production. Here’s a look at how BI contributes to optimizing key areas of the production process:
Real-Time Data Analysis
One of the most powerful capabilities of BI in manufacturing is real-time data analysis. BI platforms connect to factory floor systems and sensors to deliver up-to-the-minute data on production status. This means managers and engineers can monitor key performance indicators (KPIs) – like production rates, machine utilization, cycle time, and yield – as they happen, rather than waiting for end-of-shift reports. By visualizing these metrics in live dashboards, stakeholders can quickly spot anomalies or emerging bottlenecks and respond immediately. For example, if a particular machine’s output drops or defect rates spike, BI alerts can notify teams to investigate and resolve the issue before it impacts the whole line. Real-time visibility thus helps minimize downtime and keeps production running at peak efficiency. As an added benefit, front-line operators empowered with data can make on-the-fly adjustments, and supervisors can optimize schedules or resource allocation based on current conditions. In short, BI’s real-time analytics turn manufacturing into a proactive operation rather than a reactive one, greatly enhancing agility and throughput.
Predictive Maintenance
Equipment failures and unplanned downtime are major sources of inefficiency and cost in manufacturing. BI tools tackle this through predictive maintenance – analyzing machine data to predict potential breakdowns before they occur. By collecting sensor readings (vibration, temperature, pressure, etc.) and historical maintenance records, BI-driven analytics can detect patterns that precede a failure. Manufacturers like General Electric have employed BI-based predictive maintenance in their operations; for instance, GE continuously monitors data from aircraft engines to forecast potential failures and alert operators for maintenance, significantly reducing downtime and maintenance costs. In a broader context, BI applications in manufacturing use predictive models to forecast when a machine is likely to need service, allowing maintenance to be scheduled at optimal times. This minimizes unplanned downtime and avoids the domino effect of a sudden machine breakdown halting an entire production line. By fixing or tuning equipment just-in-time, companies also extend the lifespan of machinery and reduce repair costs, since minor issues are addressed before they become major problems. Predictive maintenance powered by BI thus keeps equipment availability high and production on schedule – a key aspect of process optimization.
Ready to optimize your manufacturing processes with Business Intelligence?
Leverage BI solutions to enhance production efficiency, reduce downtime, and gain real-time insights into your manufacturing operations. Let data drive your decision-making and unlock new levels of performance.
Our experts are here to guide you through the implementation of BI in manufacturing.
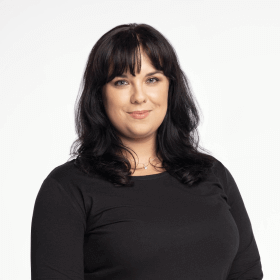
Our experts are ready to help you integrate BI into your manufacturing strategy.
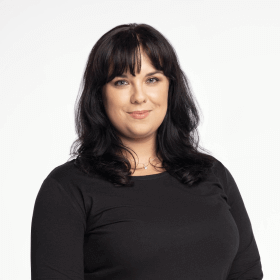
Supply Chain Optimization
A manufacturer’s efficiency is tightly linked with its supply chain performance. BI helps optimize the supply chain by providing end-to-end visibility and data-driven decision support from procurement of raw materials to delivery of finished goods. By integrating data on supplier performance, inventory levels, logistics, and customer orders, BI tools allow manufacturers to identify inefficiencies and improve supply chain operations. For example, analytics can reveal delays in shipping, inconsistent lead times from certain suppliers, or excess buffer stocks. With these insights, companies can adjust and streamline their supply chain – choosing more reliable suppliers, optimizing shipping routes, or refining order quantities. BI-driven forecasts also enable better demand planning: manufacturers can align production schedules and inventory with actual market demand, preventing both shortages and overproduction. One outcome is improved delivery times and customer service, as production is synchronized with sales needs. Additionally, optimized supply chains lower carrying costs by keeping inventories lean and reduce rush-order expenses by anticipating needs. In practice, some manufacturers using BI have cut transportation costs and improved on-time delivery metrics significantly through such analysis. Overall, BI empowers supply chain managers with real-time dashboards and predictive analytics to keep the flow of materials and products as efficient and cost-effective as possible – ensuring that production has the right resources at the right time.
Quality Control and Defect Reduction
Maintaining high product quality is paramount in manufacturing, and BI contributes by enhancing quality control processes. Throughout production, BI systems can collect data on defects, scrap rates, inspection results, and even machine settings or environmental conditions. By analyzing this data for patterns and anomalies, BI helps identify the root causes of quality issues early on. For instance, analytics might reveal that a certain production line experiences more defects during a particular shift or when using a batch of material from a specific supplier. Armed with such insight, engineers can implement targeted corrective actions – recalibrating a machine, retraining staff, or improving material sourcing – to prevent defects from recurring. BI-driven quality dashboards enable continuous monitoring of metrics like defect rates, yield, and rework, so that any deviation from quality standards triggers an immediate response. This proactive approach reduces waste and rework costs and ensures that off-spec products are caught before they reach customers. Additionally, BI tools facilitate compliance with industry quality standards by documenting trends and proving process controls are effective. Some manufacturers have integrated BI with visual inspection systems and IoT sensors to achieve near-zero defects by catching issues in real time. The result of applying BI to quality control is a higher first-pass yield, lower scrap rates, and an overall improvement in product reliability, which strengthens the manufacturer’s reputation and profitability.
Workforce Productivity
People are as critical as machines in the production process, and BI can also help optimize workforce productivity. Manufacturing BI solutions can analyze data related to labor – such as production output per worker, time taken for specific tasks, absenteeism rates, and skill levels – to provide insights into workforce performance. By tracking employee productivity and work patterns, BI tools enable manufacturers to identify where labor is being underutilized or bottlenecked. For example, analytics might show that certain assembly teams consistently finish early while others fall behind, indicating an opportunity to rebalance workloads or provide additional training. BI can also highlight skill gaps; if quality issues or slower output correlates with particular shifts or operators, managers can intervene with coaching or adjust staffing. Another way BI boosts productivity is through optimizing labor allocation: ensuring the right number of workers with the right skills are assigned to each stage of production at the right time. This prevents overstaffing (which raises costs) or understaffing (which causes delays). Some advanced BI workforce dashboards even integrate with scheduling systems to dynamically allocate workers based on real-time production needs and forecasts. The net effect is a more efficient use of human resources, where employees are engaged in the most value-added activities. By reducing idle time and overload situations, BI-driven workforce management improves morale and output simultaneously. In a data-driven factory, every worker’s contribution is visible and can be optimized – leading to higher overall productivity and lower labor cost per unit produced.
Key BI Tools and Technologies for Manufacturing
Implementing BI in manufacturing involves selecting the right tools and ensuring they mesh well with existing systems on the shop floor. A variety of BI software platforms are available, each with strengths in data integration, analysis, and visualization. Crucially, manufacturing BI solutions must integrate with production systems like ERP (Enterprise Resource Planning), MES (Manufacturing Execution Systems), and SCADA (control systems) to gather data in real time. Modern BI tools typically offer pre-built connectors, APIs, and ETL (Extract, Transform, Load) capabilities to pull in data from databases, IoT sensors, and enterprise applications, organizing it for analysis. This integration is what allows BI dashboards to reflect what’s happening on the factory floor and across the supply chain at any given moment.
When it comes to choosing a BI platform, manufacturers often evaluate solutions based on ease of use, the ability to handle large datasets (like IoT streams), real-time analytics features, and compatibility with their IT stack. Some of the popular BI tools in the manufacturing sector include:
- Microsoft Power BI – A widely used BI platform known for its user-friendly interface and strong integration with the Microsoft ecosystem. Power BI can connect to a broad range of data sources (including ERP databases and IoT hubs) and allows users to create interactive dashboards and reports. It is often favored for its relatively low cost and cloud-based sharing, making it suitable for manufacturers of all sizes.
- Tableau – A leading data visualization tool that enables deep analysis through rich graphics and dashboards. Tableau excels at helping users spot trends and outliers with its drag-and-drop interface. In manufacturing, Tableau is used to create detailed production and quality dashboards, and it can integrate with databases and spreadsheets common in operations. Its visuals can bring complex factory data (like yield by batch or defects by machine) into an easily understandable format for decision-makers.
- SAP BusinessObjects (SAP BI) – An enterprise-grade BI suite that integrates seamlessly with SAP’s ERP and manufacturing modules (a common backbone in large manufacturing companies). SAP BI provides robust reporting and analytics capabilities within the context of manufacturing operations – for instance, pulling data directly from production orders, inventory management, and supply chain transactions in SAP. This tight integration is valuable for manufacturers who already rely on SAP systems, as it ensures consistency and real-time data flow between production and BI dashboards.
- Qlik Sense – A powerful BI and data discovery tool that offers an associative data engine, allowing users to explore data freely without predefined hierarchies. Qlik is known for handling large datasets and enabling real-time analysis, which is useful for manufacturing scenarios like monitoring sensor data or tracking OEE (Overall Equipment Effectiveness) across multiple lines. Qlik Sense’s intuitive dashboards and search-based analytics help operations teams drill into data to find root causes of issues or opportunities for efficiency.
Each of these tools (and others in the market) brings something to the table, and often the choice comes down to a manufacturer’s specific needs and existing infrastructure. What’s important is that the chosen BI solution can interface with shop floor systems and databases, handle the volume and velocity of manufacturing data, and present insights in an accessible way to engineers, managers, and executives. With the right BI software in place – whether a self-service tool for plant managers or an integrated analytics module within an ERP – manufacturing organizations can continuously monitor their operations and drive improvements based on solid data. The combination of the proper BI platform and a well-planned data architecture turns raw production data into a strategic asset.
Case Studies and Real-World Applications
Real-world success stories illustrate how BI is transforming manufacturing operations. Many companies have documented significant improvements in efficiency, cost savings, and production output after implementing BI solutions. Here are a few examples and data points showcasing the impact of BI in manufacturing:
- Reducing Downtime by 40%: A global manufacturing company faced frequent equipment failures that caused unplanned downtime and disrupted production. By integrating BI dashboards with their machine data, they were able to monitor performance in real time and identify patterns leading to breakdowns. The BI solution provided alerts and visualizations that helped maintenance teams address issues proactively. As a result, this manufacturer reduced unplanned downtime by 40% and saw substantial improvements in on-time order fulfillment and reduced maintenance costs. This case highlights how BI-driven insights can directly boost uptime and productivity.
- Predictive Maintenance at GE: Industrial giant General Electric (GE) employs BI and analytics for predictive maintenance in its aviation manufacturing division. By continuously analyzing data from aircraft engine sensors (temperature, vibration, etc.), GE’s BI system can forecast potential engine part failures and recommend maintenance before a fault occurs. This proactive approach has significantly lowered unexpected engine downtime and improved safety. The initiative also cut down maintenance expenses by avoiding catastrophic failures and optimizing spare parts inventory. GE’s example shows BI’s role in handling big data (from IoT devices) and applying advanced analytics (AI/ML algorithms) to solve manufacturing reliability challenges – yielding both cost and operational benefits.
- Inventory Optimization and Profit Gains: In addition to individual company cases, industry analyses have found broad benefits from BI. For instance, manufacturers that use BI for demand forecasting and inventory optimization have been able to prevent stockouts and reduce excess inventory, leading to better customer satisfaction and lower holding costs. One study (by Gartner) noted earlier found that BI adoption corresponds with an average 8–10% increase in profitability for organizations. This comes from a combination of efficiency gains, smarter decision-making, and waste reduction across processes. Moreover, BI helps companies identify profitable product lines, underperforming areas, and cost-saving opportunities by consolidating financial and operational data. The cumulative effect is a stronger, more responsive manufacturing business.
These examples demonstrate that Business Intelligence is not just a theoretical value-add, but a proven catalyst for manufacturing performance improvements. From the factory floor to the C-suite, having timely, accurate data has empowered companies to fine-tune their operations. Whether it’s a smaller manufacturer using Power BI to visualize and eliminate production bottlenecks, or a large enterprise integrating predictive analytics into every plant, the real-world ROI of BI is evident in metrics like reduced downtime, higher throughput, improved quality, and increased profit margins. The common thread in these cases is that data-driven decision making, enabled by the right BI tools, leads to better outcomes than relying on intuition or traditional reports. Manufacturers who invest in BI often find that it pays for itself many times over through the efficiencies and insights gained.
Future Trends in BI for Manufacturing
The landscape of BI in manufacturing continues to evolve rapidly, driven by technological advancements and the growing demands for smarter, more agile production. Several key trends are shaping how BI will further optimize manufacturing in the coming years:
- Integration of AI and Machine Learning: BI platforms are increasingly incorporating Artificial Intelligence (AI) and Machine Learning (ML) to provide more sophisticated analytics. These technologies enable systems to sift through massive datasets quickly and uncover patterns that humans might miss. In manufacturing, AI/ML integration means BI tools can better predict outcomes and recommend optimizations. For example, machine learning models can improve predictive maintenance accuracy, refine demand forecasts, or even suggest optimal machine settings for quality control. As this trend grows, manufacturers will benefit from BI systems that not only report what is happening but also intelligently predict what will happen and prescribe actions. This can lead to even greater cost savings and efficiency improvements by automating complex analyses. We can expect future BI solutions to flag potential issues or improvement opportunities on their own, using AI-driven insights to guide human decision-makers.
- IoT-Driven Data and IIoT: The Industrial Internet of Things (IIoT) – i.e., the network of connected sensors and smart devices on the factory floor – is generating unprecedented volumes of data. Future BI in manufacturing will heavily leverage IoT data to provide a granular, moment-by-moment picture of operations. As more machines, tools, and even products are embedded with sensors, BI systems will integrate with IoT platforms to monitor conditions and performance in real time across the production line. This trend goes hand-in-hand with edge computing, where data processing happens near the data source for faster analytics. The result will be BI dashboards showing live feeds of machine health, environmental conditions, and production metrics, enabling instantaneous adjustments. Additionally, IoT data combined with BI analytics will power advanced use cases like digital twins (virtual models of the factory) for scenario testing and optimization. Manufacturers embracing IoT-driven BI can further reduce downtime, precisely control quality, and achieve just-in-time operations with a level of insight that simply wasn’t possible before.
- Cloud-Based BI Solutions: Cloud computing is becoming the backbone for many BI deployments, and this trend is strong in manufacturing as well. Cloud-based BI offers scalability and flexibility that on-premises solutions sometimes lack. Manufacturers are adopting cloud BI to enable access to data and analytics from anywhere – whether at corporate headquarters or on a tablet at the shop floor. Cloud platforms also simplify the integration of disparate data sources (from global plant locations, for instance) into one central repository. As companies increasingly operate across multiple sites and even implement remote operations management, cloud BI supports collaboration by making the same up-to-date data available to all stakeholders. Moreover, cloud BI vendors are rapidly adding features like AI, real-time processing, and enhanced security, making advanced analytics more affordable and easier to implement. We will likely see more manufacturers shifting their BI infrastructure to cloud services to take advantage of faster deployment and continuous updates. This move ties into broader trends of digital transformation, where cloud-based tools help manufacturers be more agile and responsive to change.
Looking ahead, it’s clear that BI in manufacturing will become more intelligent, more real-time, and more interconnected. Trends like AI, IoT, and cloud are converging to create a new generation of “smart factory” analytics. We may also see increased use of augmented analytics (AI assisting in insight generation), natural language querying of data, and AR/VR visualizations for factory data in the future. Importantly, as sustainability becomes a focus, BI will also be used to track energy usage and waste for greener manufacturing. Manufacturers that stay on top of these trends will be equipped with extremely powerful BI ecosystems, giving them an edge in efficiency and innovation in the years to come.
Conclusion
Business Intelligence has emerged as a critical investment for manufacturers aiming to optimize their production processes and stay competitive. By harnessing data from every aspect of operations – machines, people, and supply chains – BI provides the visibility and insight needed to drive continuous improvement. The case for BI in manufacturing is clear: companies that successfully implement BI solutions see tangible benefits like reduced costs, higher productivity, better quality control, and more informed strategic decisions. They are able to respond faster to problems and opportunities, basing their actions on facts and forecasts rather than guesswork. In today’s data-rich manufacturing environments, leveraging BI is no longer optional but essential. It equips manufacturers with the capability to achieve operational excellence and adapt in a dynamic market, turning potential data overload into a strategic advantage.
In summary, Business Intelligence helps manufacturers work smarter, not just harder. It optimizes production by ensuring that resources – from raw materials to machinery to labor – are used in the most efficient way possible, guided by real-time feedback and analysis. As we’ve discussed, the combination of improved efficiency, cost savings, and competitive advantage makes a compelling case for investing in BI. Manufacturers that embrace BI tools and cultivate a data-driven culture position themselves to improve not only their current operations but also to innovate for the future. By doing so, they set the stage for sustained success, leveraging the power of data to build factories that are truly intelligent and future-ready. The key takeaway is clear: investing in Business Intelligence is investing in the future of manufacturing, where informed decisions and optimized processes drive profitability and growth.
Let's talk about your IT needs

Let me be your single point of contact and lead you through the cooperation process.
Choose your conversation starter
Signed, sealed, delivered!
Await our messenger pigeon with possible dates for the meet-up.