The manufacturing landscape is experiencing its most significant transformation since the industrial revolution. As artificial intelligence reshapes production floors worldwide, 87% of manufacturers have already adopted AI or plan to implement it within two years (source). Yet here’s the sobering reality: only 14% of frontline workers have received proper AI upskilling, compared to 44% of leadership roles.
This stark disparity reveals a critical challenge facing today’s manufacturing executives. While your C-suite may be ready for the digital transformation workforce revolution, your production teams – the backbone of your operations – are being left behind.
Workforce 4.0 represents more than just another buzzword in manufacturing circles. It’s a fundamental shift in how humans and machines collaborate on the factory floor. The companies that master this workforce transformation are already seeing remarkable results: 27.6% reduction in defective products and 29.2% cost reductions through effective human-AI collaboration (source).
But here’s what separates industry leaders from laggards: successful AI integration isn’t about replacing human workers with machines. It’s about creating synergistic partnerships where workforce adaptability becomes your competitive advantage. The evolution of workforce dynamics means your team members need to develop new competencies that complement AI capabilities rather than compete with them.
For manufacturing executives, the question isn’t whether to embrace AI – it’s how quickly you can prepare your workforce for this inevitable transformation. The companies that act decisively today will dominate tomorrow’s market, while those who hesitate risk becoming obsolete.
Expert Insight: “The future belongs to manufacturers who understand that Workforce 4.0 isn’t about choosing between humans and AI – it’s about optimizing the collaboration between human expertise and machine intelligence. Organizations that invest in comprehensive workforce training today will capture the competitive advantages of tomorrow.”
Understanding Workforce 4.0: The Fourth Evolution of Work
The concept of Workforce 4.0 didn’t emerge in a vacuum. To understand where we’re heading, manufacturing leaders need to grasp the historical context that brought us here.
The evolution of workforce follows a clear trajectory through industrial revolutions. Work 1.0 emerged in the late 18th century with the birth of industrial society and first workers’ organizations. Work 2.0 brought mass production and welfare state development in the late 19th century. Work 3.0 introduced globalization with early digitalization since the 1970s (source).
Now we’ve entered Work 4.0 – characterized by high degrees of integration, cooperation, and digital technology utilization. This framework, conceptualized by the German Federal Ministry of Labour and Social Affairs, represents the fourth phase of work relations in manufacturing environments.
Ready to transform your manufacturing workforce for the AI era?
We help manufacturing companies develop comprehensive Workforce 4.0 training programs that prepare your teams for effective human-AI collaboration. From skills assessment to implementation, our experts guide you through every step.
Let us guide you through our Workforce 4.0 assessment and transformation process.
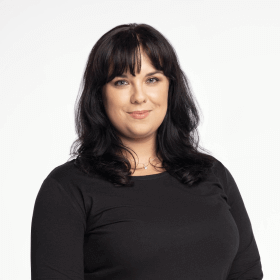
Let us guide you through our Workforce 4.0 assessment and transformation process.
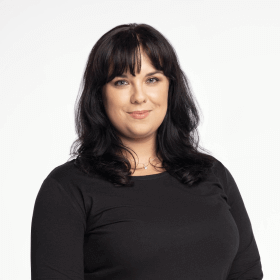
What Makes Workforce 4.0 Different
Workforce 4.0 distinguishes itself through several defining characteristics that manufacturing organizations must understand when designing training programs:
- Flexible work arrangements that adapt to both human needs and production demands
- Digital technology integration at every level of operation
- Collaborative human-machine relationships rather than competitive ones
Unlike previous industrial revolutions that primarily focused on mechanical automation, Workforce 4 recognizes that humans and AI systems must work synergistically. This collaborative approach requires workers to develop new competencies that complement artificial intelligence capabilities rather than compete with them.
The Driving Forces Behind Transformation
The transformation to industry 4.0 workforce is driven by four key factors:
- Digitalization – The integration of digital technologies across all manufacturing processes
- Globalization – Increased competition and market complexity
- Demographic changes – Aging populations and shifting migration patterns
- Cultural shifts – Growing acceptance and expectation of technology integration
These drivers create complex challenges for manufacturing organizations, including economic sector transformation effects on employment, creation of new markets through digital platforms, and the delicate balance between human and machine labor utilization.
Expert Insight: “Manufacturing leaders must navigate these transformation challenges while ensuring that upskilling efforts enhance rather than diminish human expertise and experience. The goal isn’t to replace human judgment but to amplify it through intelligent systems.”
Characteristics of Workers 4.0
Contemporary research demonstrates that workforce innovation requires workers who are characterized by:
- Adaptability to new technologies and work methods
- Digital competence for success in digital work environments
- Effective collaboration capabilities with both humans and AI systems
- Commitment to lifelong learning and continuous skill development
These characteristics form the foundation for effective AI integration training programs, as workers must possess both technical skills and adaptive mindsets to thrive in human-AI collaborative environments.
The Current State of AI Integration in Manufacturing
The reality of AI adoption in manufacturing is both promising and challenging for executives planning their workforce transformation strategies. Current data reveals a rapidly evolving landscape that demands immediate attention from leadership teams.
AI Adoption Patterns and Scale
39% of manufacturers have already begun integrating AI into production and manufacturing functions, with 72% leveraging AI and similar technologies to reduce costs and boost operational efficiency (source). This widespread adoption creates immediate training needs as organizations must prepare their workforce to operate effectively alongside intelligent systems.
The scope of AI applications in manufacturing is expanding rapidly across multiple domains:
- Predictive maintenance – Anticipating equipment failures before they occur
- Quality control – Real-time defect detection and process optimization
- Process optimization – Continuous improvement of production workflows
- Real-time decision-making support – Data-driven insights for immediate action
The Skills Gap Reality
These AI applications fundamentally alter traditional job responsibilities, requiring workers to develop new skill sets for interpreting AI-generated insights, managing automated systems, and making informed decisions based on machine learning predictions.
Expert Insight: “The challenge isn’t just implementing AI technology – it’s preparing your workforce to understand, trust, and effectively collaborate with these intelligent systems while maintaining the critical thinking capabilities that machines cannot replicate.”
Operational Impact of Effective Human-AI Collaboration
Manufacturing environments implementing AI report significant operational improvements when workers are properly trained to collaborate with intelligent systems. Smart factories utilizing effective human-AI collaboration achieve substantial reductions in defects and operational costs.
These improvements result from workers who understand how to:
- Leverage AI capabilities while applying human judgment
- Apply creativity and contextual knowledge that machines cannot replicate
- Make strategic decisions based on AI-generated recommendations
- Maintain quality standards through human oversight of automated processes
Technical Infrastructure Requirements
The technical infrastructure supporting AI integration requires workers to understand several key technologies:
- Cyber-physical systems – Integration of computational and physical processes
- Internet of Things (IoT) connectivity – Network of interconnected devices and sensors
- Data analytics platforms – Tools for processing and interpreting large datasets
- Digital twins – Virtual replicas of physical manufacturing processes
Manufacturing teams must develop competencies in managing these technologies, interpreting real-time sensor data, and optimizing processes based on AI-generated recommendations. This technical complexity demands comprehensive training approaches that combine theoretical understanding with practical application opportunities.
The Human Element in AI-Enhanced Manufacturing
The most successful implementations recognize that workforce adaptability isn’t about workers becoming more machine-like – it’s about amplifying uniquely human capabilities that complement AI strengths. Training programs must therefore focus on developing complementary skills rather than attempting to replicate machine capabilities.
Essential Skills for Human-AI Collaboration
The successful integration of AI in manufacturing environments requires workers to develop a comprehensive skill set that bridges traditional manufacturing expertise with digital transformation workforce competencies. For manufacturing executives, understanding these essential skills is crucial for designing effective training programs that deliver measurable ROI.
Digital Literacy: The Foundation Layer
Digital literacy represents the most fundamental requirement for any workforce 4.0 initiative. This encompasses comfort with computers, smart devices, and specialized software applications including:
- Enterprise Resource Planning (ERP) systems – Integration of core business processes
- Manufacturing Execution Systems (MES) – Real-time production floor management
- Digital twin technologies – Virtual modeling of physical processes
This foundational skill set enables workers to interact effectively with AI-powered tools and interpret digital information accurately. Without this base layer, more advanced AI collaboration becomes impossible.
Data Analytics Capabilities: The New Manufacturing Language
Data analytics capabilities have emerged as critical competencies for Workforce 4.0, as data serves as the primary fuel powering Industry 4.0 systems.
Your workers must develop the ability to:
- Analyze and interpret data for process improvement
- Understand how to leverage AI algorithms for predictive maintenance
- Apply machine learning insights to production optimization and quality control decisions
- Recognize patterns in manufacturing data that inform strategic decisions
This analytical competence requires training in statistical concepts, pattern recognition, and the practical application of machine learning insights to manufacturing challenges.
Problem-Solving and Critical Thinking in Automated Environments
Problem-solving and critical thinking skills become increasingly important in highly automated and interconnected manufacturing environments.
Workers must be able to:
- Troubleshoot complex issues arising from technology integration
- Think critically about process optimization opportunities
- Provide human judgment and contextual understanding that enhances automated decision-making systems
- Solve problems creatively when AI systems encounter unexpected scenarios
Expert Insight: “The most valuable manufacturing workers in the AI era aren’t those who can compete with machines, but those who can think critically about what machines can’t see – context, nuance, and creative solutions to unprecedented challenges.”
Communication and Collaboration in Cross-Functional Teams
Communication and collaboration skills take on new dimensions in Workforce 4.0 environments, where cross-functional teams integrate IT, engineering, and operations expertise.
Modern manufacturing workers must:
- Effectively communicate complex technical concepts to colleagues with varying levels of technical expertise
- Collaborate seamlessly in human-AI teams where both humans and machines contribute to decision-making
- Translate between technical and operational languages to ensure smooth information flow
- Coordinate effectively across departments that may have different AI maturity levels
Advanced Competencies for Workforce Innovation
Beyond foundational skills, workforce innovation requires additional critical capabilities:
- Virtual collaboration capabilities for effective teamwork via technology
- Cognitive load management for filtering information by importance and maximizing cognitive functions
- Computational thinking for translating data into abstract concepts
- Design mindset for task representation and process development
- Social intelligence for concept communication and reaction stimulation
- Adaptive thinking for solution development and deeper meaning interpretation
These skills create a comprehensive framework for preparing manufacturing workers to thrive in AI-enhanced environments (source).
The Strategic Imperative for Skill Development
For manufacturing executives, the message is clear: workforce adaptability isn’t optional – it’s a competitive necessity. Companies that invest in comprehensive skill development today will capture the productivity gains and cost reductions that AI promises, while those who neglect workforce preparation will struggle to realize AI’s potential benefits.
Training Frameworks and Methodologies for Workforce 4.0
Developing effective training frameworks for Workforce 4.0 requires a systematic approach that addresses both immediate skill gaps and long-term adaptability needs. For manufacturing executives, the key to success lies in implementing comprehensive frameworks that deliver measurable results while minimizing production disruptions.
Diagnostic Assessment: The Foundation of Effective Training
Research identifies diagnostic assessments as the critical first step in successful training frameworks. These assessments must examine:
- Existing skill levels across your workforce
- Technology infrastructure readiness and gaps
- Cultural readiness for AI integration
- Baseline competency data for customized training program development
Without this foundational assessment, training programs risk missing critical gaps or duplicating existing strengths, leading to wasted resources and suboptimal outcomes.
Strategic Alignment and Leadership Commitment
Leadership commitment and strategic alignment form the foundation of effective training initiatives. Organizations must:
- Develop clear vision statements for Industry 4.0 transformation
- Ensure training programs align with broader business objectives
- Secure necessary resources for comprehensive workforce development
- Demonstrate organizational commitment to increase employee buy-in and participation
This strategic alignment helps manufacturing executives justify training investments while creating the organizational momentum necessary for successful transformation.
Cultural Transformation Integration
Cultural transformation represents a critical component of successful training frameworks, requiring:
- Effective communication strategies that address worker concerns
- Employee empowerment approaches that build confidence in new technologies
- Continuous learning focus that makes adaptation part of daily operations
Organizations must create environments that embrace technological change while supporting workers through the transition process. This cultural element addresses resistance to change and fear of job displacement, creating psychological safety for learning and experimentation.
Expert Insight: “The most successful Workforce 4.0 transformations happen when cultural change and skills training advance together. You can’t train people to embrace AI if they’re fundamentally afraid it will eliminate their jobs.”
Practical Training Methodologies
Modern training frameworks incorporate diverse approaches including:
- Lectures for foundational knowledge delivery
- Audio-visual methods for simulating smart factory concepts
- Group work for collaborative problem-solving
- Hands-on experience with AI tools and systems
The integration of virtual reality (VR) and augmented reality (AR) technologies provides safe environments for practicing with AI systems without disrupting production workflows. These immersive training approaches enable workers to develop confidence and competence before applying new skills in operational environments.
Personalized Learning Paths
Modern training frameworks increasingly emphasize personalized learning paths that adapt to individual worker needs and skill levels.
Key benefits include:
- AI-powered training platforms that analyze worker progress
- Customized content delivery that accelerates skill development
- Reduced onboarding time through targeted learning
- Accommodation of diverse learning styles and existing expertise levels
These adaptive approaches ensure that training remains relevant and engaging while accommodating the diverse backgrounds and learning preferences within manufacturing teams.
Implementation Timeline and Phasing
Successful workforce transformation requires careful phasing to balance urgency with operational continuity:
Phase | Timeline | Key Activities | Expected Outcomes |
Phase 1: Foundation Building | Months 1-3 | • Diagnostic assessments and skills mapping • Leadership alignment and communication strategy • Cultural readiness preparation | • Clear understanding of current capabilities • Organizational buy-in and commitment • Reduced resistance to change |
Phase 2: Core Skills Development | Months 4-9 | • Digital literacy training • Basic AI collaboration skills • Data analytics fundamentals | • Workers comfortable with basic AI tools • Improved data interpretation abilities • Foundation for advanced training |
Phase 3: Advanced Integration | Months 10-18 | • Complex problem-solving with AI systems • Cross-functional collaboration • Continuous improvement methodologies | • Full human-AI collaboration capability • Measurable productivity improvements • Self-sustaining learning culture |
Measuring Training Effectiveness
Measurement and evaluation systems enable organizations to track training effectiveness and make necessary adjustments (source). Key metrics include:
- Skill assessment scores before and after training
- Production efficiency improvements attributed to better human-AI collaboration
- Error reduction rates in AI-assisted processes
- Worker confidence levels with AI systems and tools
Regular evaluation allows organizations to refine training programs, address emerging skill gaps, and demonstrate return on investment for workforce development initiatives.
Organizational Culture Transformation
The successful implementation of Workforce 4.0 training requires fundamental organizational culture transformation that supports technology adoption and continuous learning. For manufacturing executives, culture change isn’t just a nice-to-have – it’s a critical success factor that can make or break your AI integration efforts.
The Cultural Impact of Industry 4.0 Technologies
Research demonstrates that Industry 4.0 technologies significantly influence organizational culture traits, particularly in areas of company results focus, cooperation and dialogue, task performance, and openness to innovative solutions.
Organizations must proactively shape these cultural elements to create environments conducive to human-AI collaboration.
IT Systems Integration as a Cultural Catalyst
IT systems integration emerges as the most influential technology for organizational culture transformation, significantly affecting task completion, company results, cooperation levels, and innovation openness.
This finding suggests that manufacturing executives should prioritize integrated technology platforms when designing culture change initiatives, as these systems create the greatest cultural impact while supporting comprehensive AI adoption across manufacturing operations.
Addressing Worker Concerns and Resistance
The transformation process requires addressing worker concerns about job displacement and technological change. Research indicates that 36% of workers believe their jobs could be eliminated by AI, creating resistance to training initiatives (source).
Expert Insight: “The key to successful culture transformation is reframing the narrative from ‘AI will replace you’ to ‘AI will make you more valuable.’ When workers see technology as a tool for career advancement rather than job elimination, resistance transforms into enthusiasm.”
Strategies for Cultural Transformation
Manufacturing organizations must implement comprehensive approaches to reshape workplace culture:
Communication and Transparency
- Consistent messaging about AI’s role in augmenting rather than replacing human workers
- Transparent change management that acknowledges concerns while highlighting opportunities
- Regular updates on transformation progress and success stories
Confidence Building Through Gradual Implementation
- Gradual technology introduction that allows workers to adapt progressively
- Comprehensive support systems including peer mentoring and technical assistance
- Clear governance frameworks addressing data privacy, system reliability, and ethical AI use
Leadership Modeling and Support
- Leadership behaviors that demonstrate positive attitudes toward technology adoption
- Management coaching to support workers through AI integration challenges
- Consistent support throughout the organization while creating accountability for workforce development outcomes
Building Innovation-Friendly Environments
Cultural transformation initiatives must balance innovation with security and reliability concerns. Workers need confidence that AI systems will enhance rather than complicate their work environments.
Key elements include:
- Psychological safety for experimentation and learning from mistakes
- Recognition systems that reward adaptation and innovation
- Collaborative problem-solving approaches that value both human insight and AI capabilities
- Continuous improvement mindset that treats challenges as learning opportunities
The Role of Leadership in Culture Change
Leadership behaviors play crucial roles in culture transformation, as managers must model positive attitudes toward technology adoption while supporting workers through learning processes.
Training programs must include leadership development components that prepare supervisors and managers to:
- Coach workers through AI integration challenges
- Provide consistent messaging and support throughout the organization
- Create accountability for successful workforce development outcomes
- Recognize and celebrate progress in human-AI collaboration
Measuring Cultural Transformation Success
Organizations implementing effective cultural transformation programs report:
- Improved employee engagement in technology adoption initiatives
- Reduced resistance to change across all organizational levels
- Accelerated technology adoption rates compared to organizations without culture focus
- Higher retention rates among workers participating in AI training programs
Creating Sustainable Culture Change
The most successful workforce innovation initiatives create self-reinforcing cultural changes that sustain transformation beyond initial training programs. This requires:
Embedding Learning in Daily Operations
- Integration of continuous learning into regular work processes
- AI collaboration as a standard part of job descriptions and performance evaluations
- Knowledge sharing systems that capture and disseminate best practices
Long-term Commitment Demonstration
- Career advancement paths that reward AI collaboration skills
- Investment in ongoing training and skill development
- Recognition programs that celebrate innovation and adaptation
Organizations that successfully transform their culture create environments where workforce adaptability becomes a core competitive advantage, enabling them to navigate future technological changes with confidence and agility.
Implementation Strategies and Best Practices
Successful Workforce 4.0 training implementation requires strategic approaches that address technical, human, and organizational factors simultaneously. For manufacturing executives, the difference between success and failure often lies in following proven best practices that minimize risk while maximizing return on investment.
Data Readiness: The Critical Foundation
Best practices begin with data readiness initiatives that ensure AI systems have access to clean, well-structured, and accessible information. Organizations must:
- Standardize data across production systems to ensure consistency and reliability
- Implement real-time data collection through IoT sensors and connected devices
- Utilize cloud storage solutions that improve AI accessibility and processing speed
- Establish data governance protocols that maintain quality and security standards
This foundational work enables effective training programs by providing reliable data sources for hands-on learning experiences. Without proper data infrastructure, even the best training programs will fail to deliver practical value.
Advanced AI Implementation: The Agentic Approach
The adoption of agentic AI represents an advanced implementation strategy that enables autonomous decision-making capabilities within manufacturing systems.
Training programs must prepare workers to:
- Supervise autonomous AI systems rather than control every decision
- Handle exceptions when AI systems encounter unprecedented situations
- Make strategic decisions that guide AI system behavior and priorities
- Monitor system performance and intervene when human judgment is required
This approach reduces the need for constant human oversight while enhancing overall efficiency and productivity, but requires workers with higher-level analytical and strategic thinking capabilities.
Strategic Partnerships for Enhanced Training
Organizations implementing successful training programs emphasize partnerships with educational institutions and training providers. These collaborations:
- Inject fresh ideas into business operations and training methodologies
- Ensure training content remains current with technological developments
- Provide access to expertise and resources not available internally
- Create pathways for ongoing professional development and certification
Manufacturing companies should establish relationships with universities, vocational schools, and specialized training organizations to access cutting-edge knowledge and proven training methodologies.
Expert Insight: “The most successful manufacturers don’t try to build all training capabilities in-house. They leverage partnerships to access world-class expertise while focusing their internal resources on what they do best – manufacturing excellence.”
Flexible Online Training Implementation
Online training programs offer flexibility that accommodates production schedules and individual learning preferences. These programs enable workers to develop AI skills without extended production downtime while providing personalized learning experiences.
Successful online training initiatives include:
- Bundled AI literacy programs covering ethics, workplace applications, and technical programming
- Interactive simulations that replicate real manufacturing scenarios
- Self-paced modules that allow workers to progress according to their schedules
- Mobile-friendly platforms that enable learning during breaks or commute time
The fully online format allows workers to progress at their own pace while maintaining regular production responsibilities.
Certification Programs for Skill Validation
Certification programs provide structured learning pathways that validate worker competencies and create career advancement opportunities. Available certifications include:
- AI in Manufacturing from TU Delft
- Robotics in Manufacturing Fundamentals from the Society of Manufacturing Engineers
- Various specialized programs focusing on specific AI applications
These certification programs provide workers with recognized credentials while ensuring standardized competency levels across the organization.
Comprehensive Measurement and Evaluation
Measurement and evaluation systems enable organizations to track training effectiveness and make necessary adjustments.
Key performance indicators include:
Metric Category | Specific Measurements | Business Impact |
Skill Development | • Pre/post training assessment scores • Certification completion rates • Competency progression tracking | • Validated skill improvements • Career advancement readiness • Training ROI demonstration |
Operational Performance | • Production efficiency improvements • Error reduction rates • Process optimization metrics | • Measurable productivity gains • Quality improvements • Cost reduction validation |
Employee Engagement | • Worker confidence levels with AI systems • Training participation rates • Job satisfaction scores | • Reduced resistance to change • Higher retention rates • Improved workplace culture |
Phased Implementation for Risk Management
Successful implementation follows a phased approach that manages risk while building momentum:
Pilot Programs
- Select high-impact, low-risk areas for initial implementation
- Focus on willing early adopters who can become internal champions
- Document lessons learned and success stories for broader rollout
Gradual Scaling
- Expand successful pilots to similar production areas
- Incorporate feedback and improvements from initial phases
- Build internal expertise through hands-on experience
Full Organization Integration
- Apply proven methodologies across all relevant departments
- Establish centers of excellence for ongoing skill development
- Create self-sustaining learning ecosystems
This phased approach allows organizations to validate training effectiveness, refine methodologies, and build internal capabilities before committing to full-scale transformation initiatives.
Workforce 4.0 Transformation – Conclusion
The transformation to Workforce 4.0 represents both an unprecedented opportunity and a critical challenge for manufacturing organizations seeking to remain competitive in the digital economy. As we’ve explored throughout this comprehensive guide, successful AI integration depends not merely on technological implementation but on comprehensive workforce transformation strategies that prepare manufacturing teams for effective human-AI collaboration. The data is compelling: organizations implementing systematic training frameworks report significant improvements in operational efficiency, defect reduction, and cost optimization, validating the strategic importance of workforce preparation for AI-enhanced manufacturing environments.
The essential elements of successful digital transformation workforce initiatives extend far beyond technical training. Manufacturing executives must orchestrate a complex transformation that includes foundational digital literacy development, data analytics competency building, problem-solving enhancement, and communication skills for cross-functional collaboration. These core competencies must be supported by organizational culture transformation initiatives that embrace technological change while addressing worker concerns about job displacement and skill obsolescence. The most effective training methodologies incorporate diverse approaches including personalized learning paths, immersive technologies, and real-time AI assistance to accommodate different learning styles and existing expertise levels within manufacturing teams.
Implementation success requires strategic attention to data readiness, gradual technology introduction, partnerships with educational institutions, and comprehensive measurement systems that track training effectiveness and return on investment. Organizations must address significant challenges including change resistance, infrastructure limitations, and skills gaps through proactive risk mitigation strategies and quality assurance measures that ensure consistent training outcomes across diverse worker populations. The companies that master this balance between human expertise and artificial intelligence will emerge as leaders in the new manufacturing landscape.
Looking ahead, the convergence of generative AI, immersive training technologies, and continuous learning models will reshape workforce innovation approaches, creating more personalized, responsive, and effective training experiences. Manufacturing organizations that invest in comprehensive Workforce 4 training programs today will be better positioned to leverage emerging technologies while maintaining competitive advantages in increasingly complex and digitalized manufacturing environments. The future of manufacturing success depends not on choosing between human workers and artificial intelligence, but on developing the organizational capabilities necessary to optimize the collaboration between human expertise and machine intelligence through strategic workforce adaptability initiatives.
Let's talk about your IT needs

Let me be your single point of contact and lead you through the cooperation process.
Choose your conversation starter
Signed, sealed, delivered!
Await our messenger pigeon with possible dates for the meet-up.